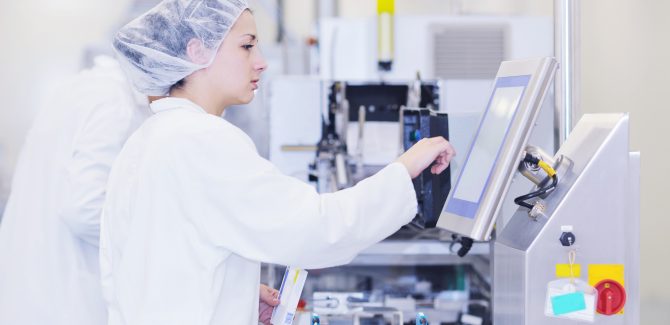
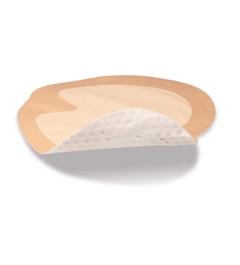
The Island Dressing Machine
The client: Brightwake is a creative engineering, development, production and research company making cutting edge developments in the world of medical, cosmetic, industrial, and aviation products.
The challenge: To design a machine that can create not just one, but a full range of dressings.
Much like 2M, Brightwake take an ingenious approach to their design and are behind many weird and wonderful products including Manuka honey infused medical dressings – this meant 2M had to consider capacity for new product development and machine evolution.
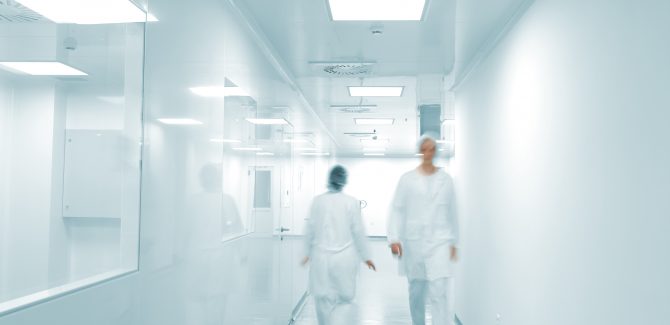
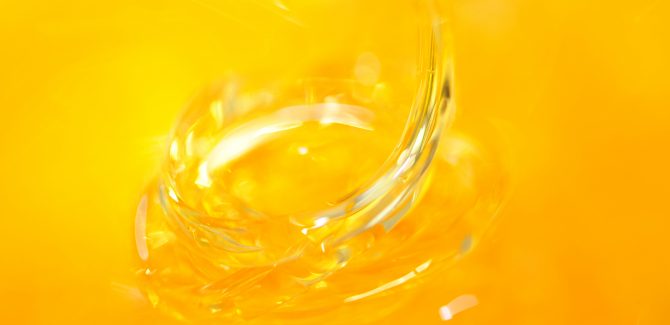
The Island Dressing Machine
Some of 2Ms work involves the consultation, testing and delivery of software behind groundbreaking research and development for products that may be years away from fully operational production.
Developing fresh ways to deliver powerful, efficient results for radical products and then testing them to the limits is something which gets the cogs whirring for the creative team at 2M.
2M have worked on many exciting research and development projects with longstanding client Brightwake but whilst they’re still in the development stages cannot go into details surrounding these products for obvious reasons. However, one project that can be divulged is their work on The Island Dressing Machine.
The outside the box bit:
The system design empowered this new machine to produce multiple profiles, which in effect means that one machine can meet the orders of multiple clients due to its newly afforded versatility.
What brought it to life?
To gain the speed, efficiency, and shear flexibility of a machine like this, a 6-axis synchronization was developed to orchestrate the movement of all the limbs of this machine, in this case control of various stages of the process.
This Mitsubishi motion control system took a life of it’s own in a sense, ensuring for now at least that the machine remains an only child. Productivity so far surpassed expectations that the planned second machine remains but a passing thought 5 years down the line.
To give an overview of the workings behind the process – the dressing materials are fed into the machine on different rollers, they’re then merged and sealed together at precise temperatures for exact timings, then shaped and cut to the order selected, before exiting the machine.
The highs and lows:
Essential to the system is the precise alignment of the central dressing panels in relation to the outer panels. The sealing of dressings must also be comprehensive without compromising the quality of the product. All of these factors are accounted for against a backdrop of incredibly high speeds and high temperatures.
The result:
The initial plan was to build a first machine then a second, but the initial project increased the efficiency of the machine to four times its previous performance and so subsequently, no new machine was needed in order to meet demand.
2Ms longstanding relationship and ongoing work on exciting research and development products with Brightwake is set to revolutionize the wound aftercare market both within hospitals and for convalescence at home and in health centres.