
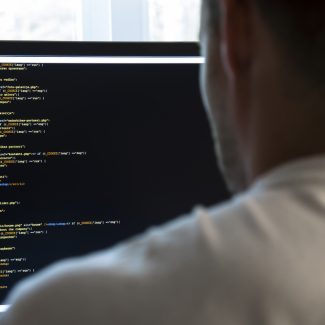
Creating A Safe Environment
One key consideration for this development was that it’s to be embedded into an explosion proof environment.
Thus, NAMUR input sensors were used. Allowing us to develop an electronic barrier, high voltage currents were isolated and low voltage current solely was allowed to pass through.
This ensures that no sparks are created and an explosion proof environment is maintained.
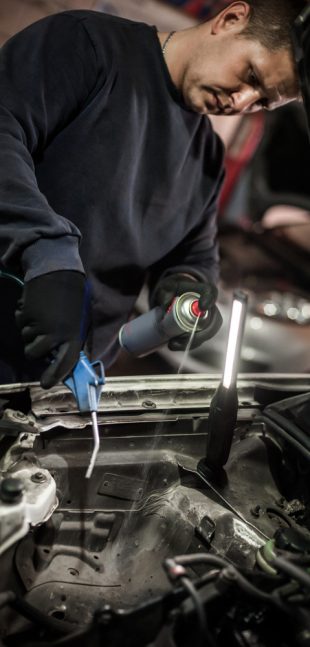

Keeping Well Oiled
WD40 is one of those rare products that most households are familiar with. It was time to develop on the fastest WD40 line in the UK with longstanding client James Briggs, as it transitioned from a pneumatic to electric control system.
The new solution also aimed to incorporate the numerous ongoing hardware upgrades – such as an automatic valve dispenser, valve checker, and the ability to run more diagnostics throughout the plant.
Ben jumped on-board this specification as his first PLC project using structured text, and the target speed was 60 cans per minute on certain products.
Ben’s highlights were seeing the machine come to life, and most challenging was the tension of adjusting code whilst the machine was in production.
“Having never thought about programming on a factory floor, it was an eye opener to experience how much of it actually goes on in that environment.”
This is an understandable reservation and puts into perspective the courage and confidence required to become fully involved on site.
It was also the latest development in a complex process chain involving multiple conveyors and lines. Pre-printed cans are brought in on stacked palettes and a layer is loaded onto the conveyor at a time.
Here ball bearings are dropped into each empty can if the job requires, e.g. for spray-paint products.
The cans are then loaded into the first station known as the filling machine. The filling machine consists of a turret into which the empty cans are fed. There are up to 6 pumps on the filling machine which combine primary colours to create the spectrum of colours required for specific product runs.
Once the cans have been fed their required doses, they’re loaded back onto the conveyor belt to Station 2 called the Crimping machine, which is again a turret which cranks round the valve placer (valve meaning the lid of spray-cans in this scenario), then onto a valve checker which verifies the valves are in their correct positions, then onto a big pneumatic crimping machine which seals the lids onto the body of the cans.
Then from Station 2 onto a conveyor whisking away cans to Station 3 which involves a gassing machine. This part of the process adds propellant where necessary (such as propane). It’s time for a bit of a spa now and cans are ferried away for testing involving a heated water-bath. This provides a mild stress test, so any can which is slightly over pressurized will burst. It also affords the opportunity to observe bubbles from any leaks.
Wishing you all plenty of rest and relaxation for the festive period – we sign out for 2019. Hoping you treat yourself as well as a can in a cozy bath if not more so! Till the new year, 2M.